Hybrid Turbochargers Explained: How They're Made And How They Work
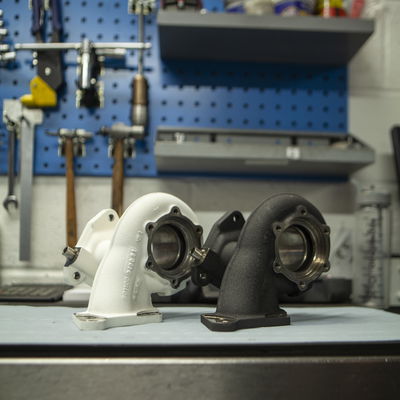
If you want more turbo performance, you could consider swapping your current unit outright for a bigger one. The only trouble is, the turbocharger itself will be expensive, and you’ll probably need to spend quite a bit more on top to get it to fit. The solution? Keep the same housing, but upgrade all the internals. This creates what’s known as a hybrid turbo.
Annoyingly, it seems the English language hasn’t kept pace with the technology being developed, so now you’ll often find electrically-assisted turbos, where an electric air compressor helps feed the conventional turbo for faster throttle response, are also becoming known as hybrid turbos. Here, we’re definitely just talking about the aftermarket.
That you can buy aftermarket turbochargers goes without saying. We’ve all known you can do that ever since we first picked up a copy of Need for Speed. Brands like HKS and GReddy have basically been stencilled onto the insides of our skulls along with all that other incredibly useful stuff about cars.
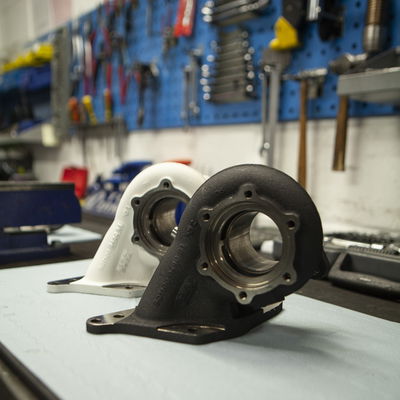
Installing one, though, isn’t always easy. If you’re lucky it’s a straight swap; other times you need metalwork and plumbing qualifications if you want to get it right. Larger turbos can force you to relocate a bunch of other things in your engine bay, which is a nightmare of custom mounting brackets. If you’re really unlucky and the bay is especially tight for space, every time you move something, yet another thing needs to be shifted slightly…
Then there’s the issue of cost: a decent turbo upgrade can sit there laughing at you from somewhere well into four figures, and that’s before any fitting costs. If you want to add extra pipework, cooling systems or other made-to-measure extras, it gets frighteningly pricey.
That’s where hybrid turbo tech comes into play. By using the existing pipework and snail casing, you remove the need to modify the engine bay. But by enlarging the compressor wheel/turbine, fitting better bearings and/or porting and polishing the housing, you can make sure you’re getting the best from your existing setup. More power will be yours, and from a glance under the bonnet no one would be any the wiser.
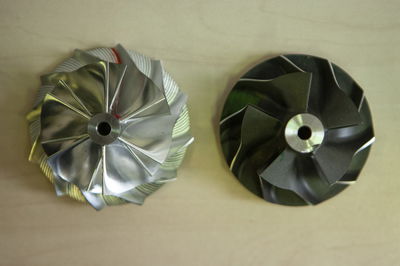
Another benefit is that the stronger turbo innards can handle more power more comfortably than the standard parts. It makes sense if you’re also planning a hefty remap, but be sure the rest of your drivetrain can reliably handle more serious power.
It’s worth mentioning that this route does come with some provisos. Firstly, the gains you’re likely to see with a hybrid turbo will always be lower than if you were to throw a big lump of cash at the issue and fit a bigger aftermarket turbo along with upgrading all the associated systems.
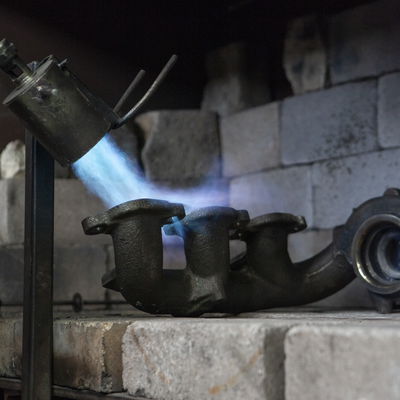
Secondly, there’s the reliability of the turbo housing and pipework. You need to be sure that those stock parts can take the extra power. Failures are uncommon, though.
Finally, it’s likely you’ll need to have the inside of the compressor housing machined out to fit the bigger turbine.
Other than that, it’s a win-win scenario. The combination of a standard look with more power sounds tempting, right?
Comments
OMG do you really get paid for this bs? Pictures of turbine housings and some compressor wheels? WTF are you smoking? It’s called an electric turbo and it only had a compressor section. Electronics cannot be near the exhaust. That’s the engineering issue. Your article is just a bunch of crap. gabedude
What are you talking about? What do you mean by electronics near the exhaust?
Pagination