Engineering Explained: A Dummy's Guide To Valvetrains And Which Design Works Best
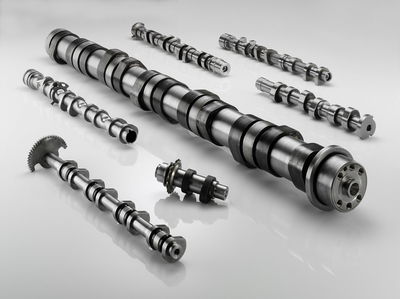
An engine is only as good as the design allows for it to breathe. Restrict airflow, and power results crumble. With that in mind, valvetrain design plays a critical role in optimising an engine’s power output and efficiency. Most modern engines fit within the categories below:
- Overhead Valve or Pushrod (OHV)
- Single Overhead Cam (SOHC)
- Dual Overhead Cam (DOHC)
- 2, 3, 4, and 5 Valves Per Cylinder
1. OHV
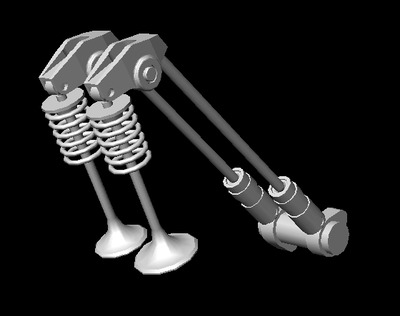
Overhead valve simply means the valves on the engine are located above the cylinder head, but it’s commonly used to refer to pushrod engines which place the camshaft lower and use lifters with pushrods to actuate the valves. Despite the old-school nature to the design, there are inherent advantages.
Advantages
- With V-shaped engine blocks, placing the camshaft within the V makes for an extremely compact design versus an overhead cam design. Not only does this keep the centre of gravity low, it helps free up space for other goodies in the engine compartment. Perhaps this could lead to more flexibility for the suspension design, or the ability to push the engine back for better weight distribution.
- Though there are additional parts used versus DOHC, there can also be parts saved. Rather than using four camshafts on a V8 engine block, just one can be used. Direct gearing to run the camshaft can sometimes be used as well since it is much closer to the crankshaft, rather than relying on a timing belt or chain.
Disadvantages
- Most pushrod engines use two valves per cylinder rather than four, as it’s fairly complex to achieve a four-valve OHV design. Using two valves can limit airflow at higher RPM.
- When using two valves, often the valves are so large that a central spark plug is not possible, as is the case with four-valve designs. This can lead to a less efficient combustion process, or the need for two spark plugs in every cylinder adding complexity.
- The reciprocating mass of the pushrod can be eliminated through OHC designs.
- Larger valves in two-valve setups have more reciprocating mass, requiring stiffer valve springs and making valve float more common, making it challenging to reach relatively high RPMs.
2. SOHC
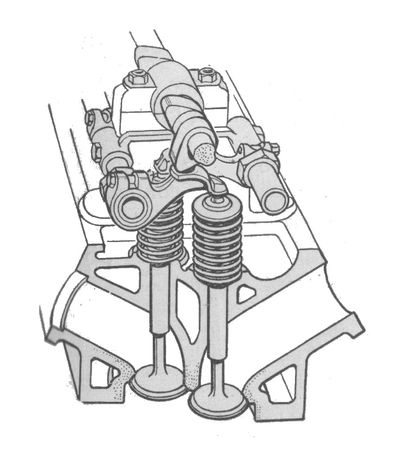
Placing the camshaft on top frees up a lot of design flexibility with the cylinder head. A four-valve setup is now much easier to implement, with all of the added benefits of doing so.
Advantages
- Simple to implement four valves per cylinder, which allows for greater airflow at high RPM.
- SOHC has also been used with two valve-per-cylinder engines, with the benefit of eliminating reciprocating pushrods.
- Saves on cost and complexity versus DOHC (and can with pushrods as well).
- Placing the camshaft on top of the cylinder head makes it more accessible for maintenance in the case of V-shaped blocks.
Disadvantages
- Doesn’t take full advantage of the airflow benefits of a DOHC design.
- Many of the same disadvantages as OHV designs for two-valve setups.
- Engine size vs OHV.
Adding another camshaft in the mix allows for the most amount of design flexibility, and it’s arguably the easiest way to implement four valves per cylinder. With two camshafts on every cylinder bank, the intake valves and exhaust valves are controlled by their own individual camshaft.
Advantages
- Easy to implement four valves per cylinder.
- Independent control of the camshafts allows for variable valve timing on both intake and exhaust, optimising airflow across a wider rev range.
- Variable valve lift is easier to implement, allowing for greater airflow at lower RPM (and higher RPM) versus a set-lift camshaft.
- Camshafts are typically more accessible versus OHV designs.
Disadvantages
- Cost and complexity.
- Size (and often weight) in comparison to OHV designs.
4. What About 2, 3, 4, Or Even 5 Valves Per Cylinder?
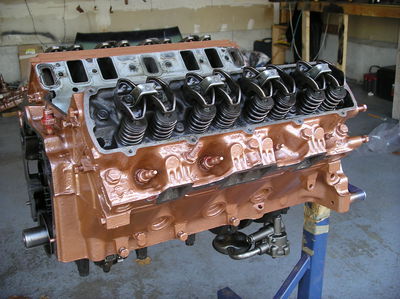
Over the years automotive manufacturers have tried various combinations of valvetrains and valve counts. While almost any combination of valves is possible with any valvetrain, the majority of engines today are DOHC with four valves per cylinder. A few companies do continue to use OHV setups, and generally with two valves per cylinder. Normally, the intake valves will be slightly larger than the exhaust valves, as it’s easier to push out the high pressure exhaust gases than pull in the relatively low pressure atmospheric air for the intake stroke.
2 Valves
Fewer moving parts is generally always a good thing, but in the case of two-valve designs the valves are often large and heavy, requiring stiffer valve springs and resulting in valve float at high RPM. This limits top-end airflow. That said, low-end torque is often better (versus four-valve setups) as the airflow is faster at lower speeds as a result of the restricted design. Even though this is generally true, there are ways to mitigate this with four-valve designs.
3 Valves
It’s not uncommon to see SOHC designs with two intake valves and one exhaust valve per cylinder. Perhaps an awkward phase into four-valve heads, this improves top-end airflow versus the typical OHV.
4 Valves
A higher valve count means better top-end airflow, as the video above mathematically demonstrates. It also allows for lighter valves reducing valve float with softer valve springs. Low-end torque can be compensated for by using variable valve lift, timing, or even variable intake manifolds. Some designs will even open just one intake valve at lower RPM, such as three-stage VTEC.
5 Valves
More is always better, right? Add on another intake valve for the ultimate free-breathing design. So why not six, 12, or 20 valves? With every additional valve, cost, complexity, and reliability are challenged, all with diminishing returns. Expect most cars to remain at four valves for the foreseeable future.
Comments
VW’s 1.8t engine in the mk4s ran 5 valves a cylinder. love that weird engine. i know it was copied off of a Suzuki motorcycle engine headhttp://i.ebayimg.com/00/s/OTA3WDE0NjU=/z/XRAAAOSwcu5URTPo/$_35.JPG?set_id=880000500F
VW 1.8ts in the mk4 gen had 5 valve per cylinder. god i love those weird engines. I know they were based off of a Suzuki motorcycle head design which makes it even werider.
I have an Audi 4.2 V8 with two heads that look like this, and 40 valves. Sounds great.
I like my simple old SOHC V6, revs over 7 grand and has a central spark plug. No valve float and plenty of air at top end. Super simple to change stuff. Cams slide in like they would in a OHV block so there are no cam bridge issues. They did good for a 30+ yr old engine.
I know from experience the downfall of a DOHC 3V engine. My 2005 F-150 has the 5.4L 3V V-8 and the variable valve timing system is problematic for those engines, leading to mine going out and needing to be replaced.
It’s not all bad though, when the system works it works great, changing the timing for optimal low-end and high-end torque, when it doesn’t work though…that’s when it sucks.
Can you do a segment on brake boosting please? I cannot figure out how to contact you.
Pagination