Here's How The 1997 Aisin Factory Fire Changed The Auto Industry
In today’s fast-paced commercial environment, supply chain management is an incredibly precise and complicated science that presents a challenge to even the greatest logistical experts. If you ask me, it’s called a supply chain because all you need to do is break one link to render the whole thing useless. As the dawn broke on February 1st, 1997, two major Japanese automotive titans would be faced with the task of preventing a supply chain crisis from turning into an economic disaster.
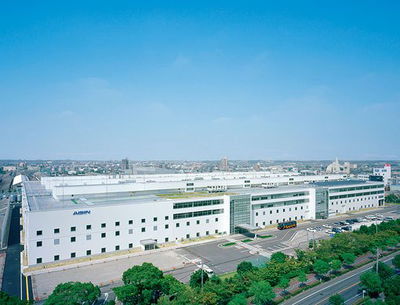
On that chaotic Saturday, a fire broke out at the Aisin Seiki Corporation’s Factory #1 in the Japanese city of Kariya. By 9:00 A.M, the assembly lines dedicated to making P-valves, a crucial component of the brake system, were completely obliterated. Aisin’s primary buyer of P-valves at the time was Toyota. This seemingly external variable would ultimately invite catastrophe in the most ironic of ways.
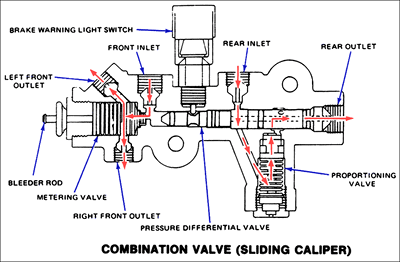
If you’ve taken any business classes in college, you might have heard of Toyota’s revolutionary manufacturing philosophy called lean. Lean is centered around the idea of minimizing waste and inefficiency in the production process, and is the central tenet of the Toyota Production System (TPS). A critical feature of the lean process is something called Just In Time inventory. This process is fairly self-explanatory—inventory only arrives to the production facility as it’s needed. In other words, all the parts arrive at the factory just in time.
Although Just In Time is extremely effective in streamlining the supply chain, it carries a risk that was made all too clear for Toyota in the wake of the Aisin fire. Since Toyota had next to none of these $5 parts in inventory, their entire manufacturing operations would grind to halt in a matter of hours. What’s more, since it would almost certainly take months for Aisin to get back into P-valve production, it seemed inevitable for Toyota’s production to grind to a halt for weeks. If that were to happen, the economic damage would have had negative consequences for both Toyota and the Japanese economy.
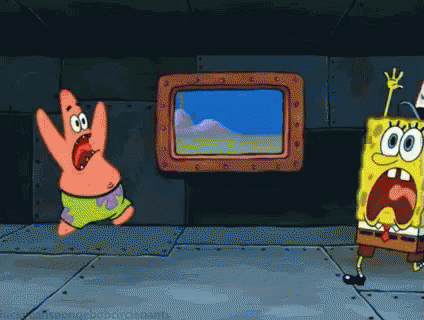
Not surprisingly, the head offices of Aisin and Toyota in full-blown crisis mode. Both companies worked together around the clock to come up with a solution. It soon became clear that the only way to avoid an economic nightmare was to try and get help from their vast network of suppliers and manufacturers. It was a crapshoot, but it was all they had.
In a world where manufacturing is a business run down to the margin, prioritizing the production of P-valves was a lot to ask of Toyota’s suppliers. Incredibly, however, they came in clutch. The first P-valves were delivered to Toyota factories on the following Wednesday, just four days after the Aisin fire. Although many experts predicted that Toyota would be crippled for months after the fire, the company resumed production in less than a week.
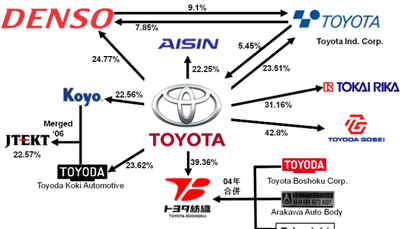
For the suppliers who worked their arses off to save Toyota, coming to the rescue was more than just an act of kindness. In fact, it was the logical response under the Japanese system of keiretsu. Keiretsu is a philosophy of business in which companies have diverse and interconnected relationships with one another. This increases the stability of each company and provides economic incentives for individual companies to be loyal to their “network”.
In other words, if Toyota’s suppliers would have said “no, thanks” during the crisis, they would have lost an extremely valuable customer after the fact. Nonetheless, Toyota and Aisin graciously rewarded the generosity of their suppliers by compensating them for their troubles, and then some.
Although the 1997 Aisin fire was still a disaster for both Aisin and Toyota, the response by both companies became a textbook example of the importance of good business relationships. The Toyota Production System and the Just In Time system of inventory withstood the crisis; and are still widely influential in manufacturing processes around the world. Considering that this system had faced the worst-case scenario, the relatively happy ending would ultimately have a profound impact on automotive manufacturing as we know it.
An Ecarnomics blog.
Comments
Never knew id have fun learning about economics
I’m going to an economics lecture soon. Should I show this comment to my professor?
*ecarnomics
Japan is such a great place. Anywhere else and the suppliers would say no simply to save themselves.
Oh yes, and Japanese business culture entails such high levels of respect. Sure, if you know anything about game theory, you can say that they did what was best for them from an economic point of view, but I like to think that long-run profits had nothing to do with that act of generosity.
Anywhere else and the suppliers would say no simply to save themselves
Simply not true. JIT forms of production are not exclusive to Japan, nor are good business relationships.
The automotive sector version of: Bro, I got you. Dont worry.
Pretty much! Hahaha
Aisin’s rebuilt factory in Kariya, Japan. All the these words seem like a playoff of other oriental words. Aisin=Asian, Kariya=Korea only in Japan would they spell it different. (NO RACISM intended) just seems funny
The definition of true friendship
Currently studying business management, coincidentally we talked about Toyota’s JIT system and Kaizen strategy just last week. Definitely worth a follow!
I met Chihiro Nakao the other day for an engineering project. He actually was a big part of the lean process and it was pretty awesome learning some things from him.
See what being a little neighborly can do, good connections can protect your ass from bein’ grass!
I got a lesson in Kaizen by Chihiro Nakao the other day at school for my engineering project. Ironic how he was very involved in the lean and moonshine process for TPS.
Where can you write a resumes?
for the right remplates, and best designs visit our site:
https://www.cnbc.com/2019/04/09/stressed-about-resume-what-to-know-before-hiring-a-professional-writing-
service.html
Where can you write a resumes?
for the right remplates, and best designs visit our site:
https://www.cnbc.com/2019/04/09/stressed-about-resume-what-to-know-before-hiring-a-professional-writing-service.html