How Electric Power Assisted Steering (EPAS) Works, And How It Compares To Hydraulic
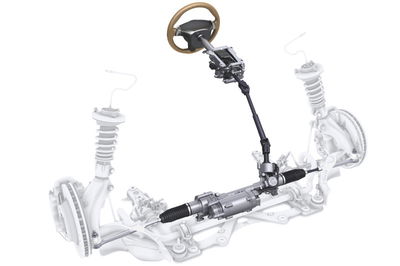
A long time ago, before the days of power steering, a steering rack was one of the most analogue systems on a car. Using a rack and pinion, simple mechanical rotation and pure arm strength was all it took to get the car pointed in your desired direction.
Then, hydraulic power steering came along, cutting strain on biceps everywhere for decades to come. In short, a hydraulic pump is powered by a belt, itself driven by the engine, which then moves a power ram with hydraulic fluid. That’s done to reduce the effort needed to steer the car.
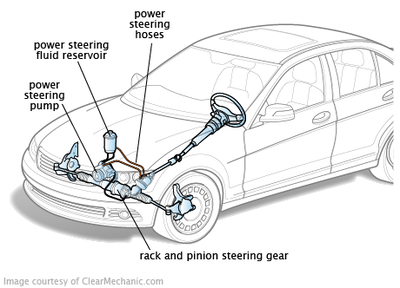
Hydraulic systems aren’t totally extinct on new cars, but electric systems have become more commonplace in recent years. So, how does electric power-assisted steering (often referred to as EPAS) work, and what are the pros and cons? We explain.
How does EPAS work?
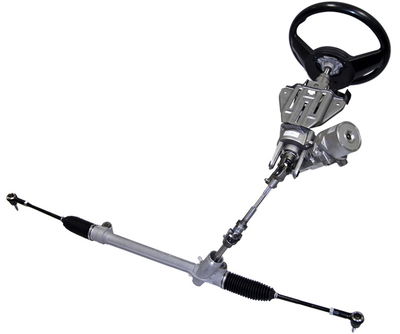
EPAS switches a hydraulic steering pump for electric motors, as seems to be the trend with pretty much any form of mechanised technology in the last decade or so.
Motors are usually placed at the base of the steering column or directly on the rack itself. Sensors then pick up the amount of steering lock being applied, and then add a proportional amount of force to the input.
Think of it a bit like the opposite of a sim racing wheel. Whereas they use electronic motors to add force and weight to a wheel, the ones on an EPAS system aim to reduce the force required to turn a car.
Why use EPAS over a hydraulic system?
Simplicity is the main thing here. Motors and sensors are easier to maintain, generally more reliable and often weigh less than all the bits required to make hydraulic power steering work.
There’s also the benefit of no parasitic losses from the engine. With hydraulic systems taking drive from a belt, an engine will have to sacrifice a little bit of power to make it work. It’s generally minute, but something is worse than nothing.
Are there downsides to EPAS?
As with many modern car technologies, there’s no rational reason for it to be considered a worse system than hydraulic power steering.
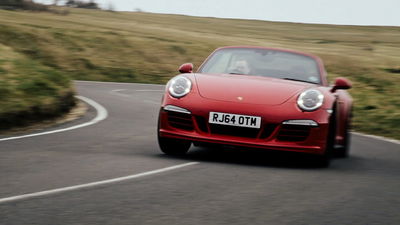
Irrationally, though, for those of us who like driving and enjoy things like feeling what the car is doing, you lose some of that connection. Forces don’t return back through an electronic system in the same way they do a hydraulic one (nor none at all, if we go really far back), and naturally, that means a car generally feels more digital to drive. Not ideal for something like a sports car.
Some manufacturers do a more convincing job than others are returning some of that. Porsche, for example, has done well to bring its EPAS system a bit of life. It really comes down to personal preference, though.
Comments
Nope, i’ll stick to my semi-assisted hydraulic steering thanks. I like being able to feel which way the wheels are pointing instead of guessing
Michael, as much as I agree with you on this post, I still think that you’ll ruin the car if you fitted electric instead of hydraulic. Take Ford’s new Mondeo/Fusion for instance.
Not my meme, but applicable.
Haha makes me remember this : https://www.carthrottle.com/post/wmrqzy5/
Rofl, i find this especially funny as my ford doesn’t have power steering.
holds up finger I CAN RELATE AND IM NOT EVEN DRIVING THE THING YET
no thank you! I consider myself a manual steering purist, even hydraulic power steering to me doesn’t give nearly as much wheel feedback as I get from manual steering, and just feels dead to me. Anyone agree?
If you have purely manual steering then the reduction ratio in the steering gear is high. Much less chance of feedback that with a well setup electrical system. I agree that some are pitiful, especially those where assistance if provided to the steering column rather than to the rack. I can’t be bothered with heavy steering.
Infiniti Q50 was the first production car to have no physical connection between the steering wheel and the wheels - a steer by wire system. Obviously this system can only ever have artificial ‘feel’. Also I always wondered what would happen if the electrics or the motor failed. There must be a fail safe but I’m not convinced.
http://www.caradvice.com.au/264587/infiniti-q50-recalled-potential-loss-steering-control/
According to this there are 3 ECU’s controlling it, but it still has issues. Personally I would never buy a car that had no physical connection for steering or brakes.
You mean Infiniti right?
Thete is a phsical connection if the steerik goes. Kinda destroys tge point thiugh
It’s sh*t.
steering in kia’s are awful fully electric
Engineer lately are leaving too much trust on these systems to the point someday there won’t be any physical link between the device (brakes, accelerator, steering, etc) and the controller (the driver itself) for the sake of fuel economy or “safety”.
You, as a driver, are not suppossed to “give away” control, it should be the opposite.
Specially on a machine that is capable of running over someone.
not all cars need driving feel, for eg:7 series
Well true, but most of us talk about the performance cars that do require.
The Engineer in me loves electric steering, but having driven some electric steering cars before I can say the lack in feel is ridiculous. It’s like you’re on ice.
Pagination